History of Pioneers – Dry Chemistry Testing
Small size, rapid testing and low-cost achieved: The SPOTCHEM EZ
Development started with questionnaires
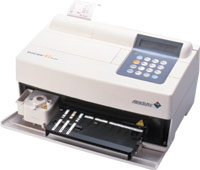
clinical chemistry
SPOTCHEM EZ SP-4430
“Let’s build an automatic dry-chemistry device that is smaller, faster and cheaper!” The development of the SPOTCHEM EZ started to achieve this. In order to put it into practice, we set about distributing questionnaires to each and every domestic customer. We found that a majority of customers were performing measurements one sample at a time and that they were using a combination of a multiple test strip and a few single test strips.
So we decided to drastically change the specifications of the existing devices. In order to achieve these first objectives, we managed to achieve the goals of single sample aspiration for continuous application on the strips, use of an LED light source and an AC power adaptor.
Out of all of these achievements, the integrated micro centrifuge is especially worthy of mention.
The road to completion of the micro centrifuge
During development of the micro centrifuge we tested many different types of centrifuge method. After a series of experiments we found that the centrifuge with swing bucket would be the most appropriate for the SPOTCHEM EZ. That was the easy part.
With the swing-out centrifuge, there were problems of the center of gravity shifting during the period of centrifugation. Also when centrifuging a single sample, it is standard practice for the customer to position a counterbalance of the same weight as the test sample, opposite it (as a balancing device). However, in this device, to place the balancer would make the operation complicated, there was a risk of losing or damaging the balancer and it was simply not practical. Also, the permanent setting of a balancer to the centrifuge rotor led to durability problems.
So one team member proposed a design of the centrifuge rotor with an irregular shape and an incorporated mass equivalent to the counterbalance weight into the centrifuge rotor itself. Then a centrifuge would need to accept different sample volumes to be placed in the centrifuge, which was not satisfied by standard design. The development team therefore began to design a totally new centrifuge to enable smooth rotation of centrifuge rotor in the entire range of acceptable sample volume.
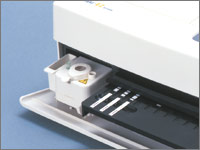
and cost for pretreatment
of samples
To do this, it was necessary to have a design to test multiple measurement items simultaneously. The calculations for obtaining results of multiple items were difficult to make and was not without complications.
Luckily, the company ethos was such that the latest design technology could be introduced and the latest three dimensional CAD had been brought in and its calculation tools were used for the more difficult calculations. This is how the built-in micro centrifuge on the market at the moment, was completed.
Synergy using software
We thought about the fact that “if the balance is off, we cannot raise the number of revolutions” from the other end: “the number of revolutions is not increased because the balance is off so this is either because of the insufficient sample volume or the absence of centrifuge container. From the number of rotations in the initial rotation period, we established a number of rotations to be reached. We designed software to detect insufficient sample volume error (or a no centrifuge error) when the set number of rotation was not reached, allowing a user to quickly find a problem. These great inventions could not have occurred without the twin blessings of our excellent team members and such a good environment for development.
First New Device Advancement Award (Prize of "President of Japan Society for the Promotion of Machine Industry")
Ever since its launch in the summer of 2000, the SPOTCHEM EZ has received very high praise from customers.
In 2004, it received the New Device Advancement Award (Prize of “President of Japan Society for the Promotion of Machine Industry”) under the auspices of the Japan Society for the Promotion of Machine Industry Technical Research Institute.
The basis for this award was that it was an automatic desktop analyzer that can be used easily even in small clinics and it has a small centrifuge built-in thus automating a lot of previously troublesome preparation.
As a result, compared with traditional devices, its focus on small size, light weight and low energy consumption received a lot of praise.
A Brand New Product Concept: the SPOTCHEM D-Concept
Development Codename: Dekki System
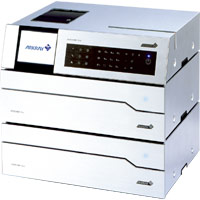
The development of the SPOTCHEM D-Concept began with an idea to create a common platform for various medical testing devices. The developing team members had many discussions on the idea of completely standardizing the parts designed for each model such as the operation part, printer, communication, which had been independently designed for each of the previous models. Finally we determined a concrete development concept: measurement units like components whereby we could develop a system like a hi-fi (called “dekki” in Japan), where the customer could choose which unit combination he or she wanted.
With this concept, the development of the Dekki System got into full swing. This is how the customizable POCT system, completely new to customers, came into being.
Keywords: Design, Component and Network
In order to provide a brand new product concept, the design team came up with the developmental keywords design component and network.
Design
Create an innovative design that casts aside the image of previous medical testing devices and is suggestive of a high-end consumer appliance.
Component
Think of componentization which allows the users to choose and connect measurement units based on their needs. A unit can be stacked on top of another so a newly added unit will require no extra space for installation. It was thought that the device’s small footprint would be a big incentive to customers for whom space is a concern.
Network
Improve remote monitoring system, which had been tested in previous models, to be available with the new device to provide higher value service with the use of our network.
With these keywords as a base we derived a concrete product image with which we could move ahead into the development of a unique system never before seen.
Overcoming problems unsolvable by extrapolating from existing products
The development of a completely new system was a battle against problems that did not occur with the development of systems similar to but better than currently available models. For example, to apply for marketing authorization required the testing of each combination of units, which would, in the previous method, take up a large number of man hours and significantly inflate costs. Two such problems were how to keep the labor and cost down and also, the need for not only experience, but also applied skills. Also because the design of the device was completely different from any previous ARKRAY products, our accumulated know-how was of no use in certain areas such as the surface finish of the keypad and the outer coating, so it was very difficult.
The mechanical system developers had to employ a significant amount of trial and error in their work and the software developers too, had to deal with many problems. How can we attain the goals of expandability and versatility and at the same time user-friendliness? We also struggled with how to maintain design versatility with given limited resources such as memory size and CPU performance for the new measurement units to be developed and connected in the future. We began to find more and more problems that we had not faced when developing conventional stand-alone models. We had many ideas and techniques in more intangible areas such as software to overcome one problem after another.
Componentization was a superb concept which seemed that anyone could have come up with but nobody had actually. Without the flexible ideas and the passion of the development staff, this would not have become a reality.
Challenges, frustrations and challenges again
Eventually we completed a prototype device and finalized design and product specifications. Then there was a pertinent remark in one of our internal company meetings.’The height of each unit is too high. When considering the use by stacking one on top of another, the commercial viability of the device both in the sense of design and the operability, will be reduced’. Mechanical system developers immediately set about looking at how to reduce the height. We found that we would have to make more changes and redo more evaluations than we had expected and we also realized that we needed to completely revise our schedule. We also had several problems remaining with the D-Concept system. With the immunological analysis unit D-01 residual liquid adhering to the end of the tip caused residual liquid contamination, which lowered the measurement precision below the required level. After several trials and errors to solve this problem, a member made a breakthrough of the entire situation. He designed a device for pushing tip point into contact with a groove (already made on the reagent pack) to draw off the residual liquid and this invention was patented. In order to fit the biochemical analysis unit D-02 into the stacked system, we found that a problem with getting access through the underside, (which he had done with conventional models) to the optical unit for cleaning as part of maintenance. We brainstormed this problem and got a novel idea of using cleaning paper.
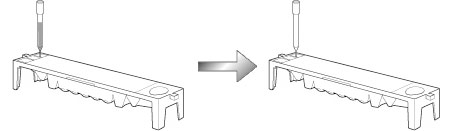
The reagent pack has a groove at one end.
Residual liquid on the end of the tip is drawn into the groove.
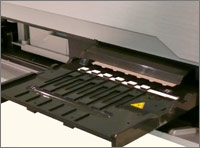
Ever since its launch in the summer of 2000, the SPOTCHEM EZ has received very high praise from customers.
Cleaning paper was used in the form of an absorbent pad like reagent pads on the multiple test strip.
When a vessel containing distilled water was set inside the device and the start key was pressed, the distilled water was applied on the cleaning paper. Then the wet cleaning paper pad was moved back and forth over the optical window to automatically clean it.
We had tried even unusual ideas with a positive attitude ‘don’t knock it until you have tried it, so let’s give it a go’, and solved problems in this way. The D-Concept was able to bounce back even stronger from the frustrations that it suffered.
And so, to the real D-Concept
When the D-Concept was visibly nearing completion, we faced still large problems in transition to the manufacturing phase. The quality of individual parts was unstable, assembly of the unit was difficult, and the inspection criteria were not determined yet. There were areas which we thought we had adequately addressed but the effect from cumulative immediate changes caused communication problems between the development team and the factory. In the face of the manufacture of a completely new system, people in charge of manufacturing could barely hide their confusion and uncertainty.
Yet the devotion of members on both the development and manufacturing side filtered through and ultimately development and factory became one in working toward a common goal.
During the process of developing the D-Concept various individuals working on different tasks grew together with one purpose to create the D-Concept. The new system development allowed connected use of several testing devices while creating a number of human connections. This can be another true meaning of D-Concept achievement.